The durability and abrasion resistance of navy water-proof fabric are paramount issues in the design and manufacturing processes. Military personnel often operate in worrying environments, encountering tough terrain, sharp gadgets, and hard situations. To meet those challenges, manufacturers hire several techniques to decorate the sturdiness and abrasion resistance of navy water-resistant cloth.
1. Material Selection:
The preference of base substances is fundamental to the overall performance of army water resistant material. High-strength synthetic materials, such as nylon and polyester, are normally used due to their inherent resistance to put on and tear. These substances offer a robust basis for the cloth, making sure it can resist the trials of army operations.
2. Reinforcement Technologies:
Manufacturers combine reinforcement technologies to strengthen unique areas of the material that are greater prone to abrasion. This can involve adding greater layers of cloth, reinforcing fibers, or incorporating technologies like ripstop, which prevents small tears from spreading and compromising the material's integrity.
3. Coating and Laminating Processes:
Waterproof fabric regularly go through coating or laminating techniques to beautify their sturdiness. These procedures involve applying a defensive layer to the material's floor. Polyurethane (PU) and polytetrafluoroethylene (PTFE) coatings, as an example, create a barrier towards abrasion whilst retaining flexibility and breathability.
4. Durable Water Repellent (DWR) Treatments:
DWR treatments are generally applied to navy water-resistant fabric to enhance water resistance and save you saturation. Additionally, DWR remedies make contributions to abrasion resistance by way of lowering friction among the fabric and external elements. This not most effective complements the cloth's lifespan but additionally guarantees most desirable performance in wet conditions.
5. Seam Construction:
Seams are ability vulnerable factors in any material, and addressing this vulnerability is important for durability. Military waterproof fabrics frequently characteristic strengthened seams, and manufacturers use specialised seam-sealing strategies or tapes to save you water ingress and enhance the general structure.
6. Testing and Quality Control:
Rigorous checking out techniques are employed in the course of the manufacturing manner to evaluate the fabric's sturdiness and abrasion resistance. This consists of abrasion resistance tests, wherein fabrics are subjected to managed abrasion to simulate real-international conditions. Quality control measures make certain that only substances assembly specified standards are used in the production of military water-resistant cloth.
7. Research and Development:
Ongoing research and development efforts play a pivotal position in enhancing the sturdiness of military waterproof fabrics. Manufacturers invest in innovation to explore new substances, coating technology, and production methods that may in addition decorate abrasion resistance without compromising other important characteristics consisting of breathability and versatility.
8. User Feedback Integration:
Feedback from military employees in the field is beneficial for producers searching for to always enhance their merchandise. Insights from real-international utilization help become aware of areas for enhancement, main to iterative improvements in the layout and creation of military water-proof fabric.
In end, the durability and abrasion resistance of navy waterproof cloth are executed via a aggregate of advanced materials, strategic reinforcement, coating technology, and a dedication to rigorous trying out and non-stop improvement. The collaboration between fabric scientists, engineers, and end-users ensures that those fabrics now not only meet however exceed the worrying necessities of military operations in rugged environments.
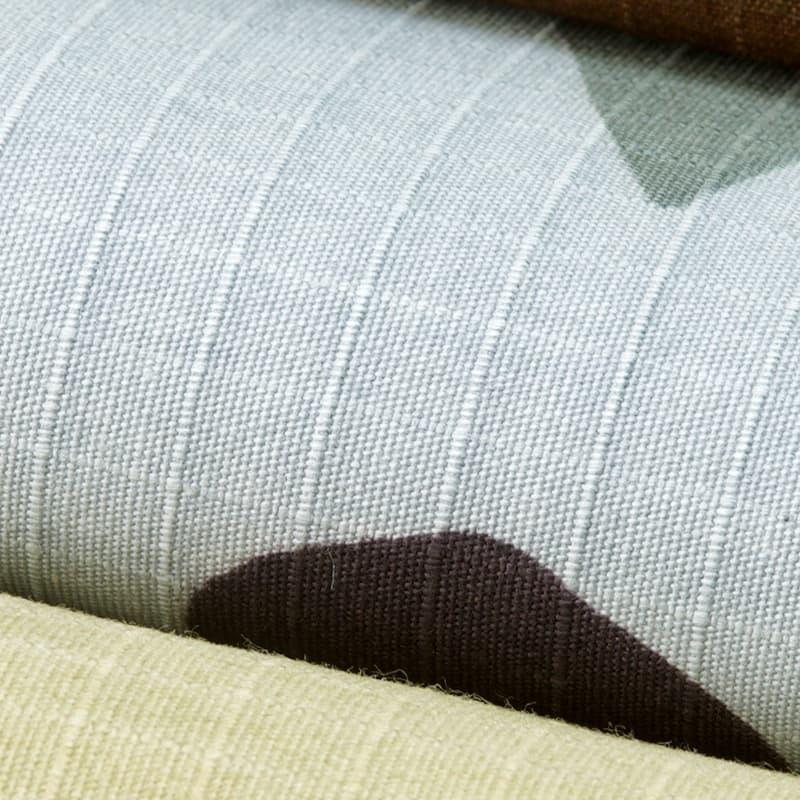
Waterproof Camouflage Coating Fabric
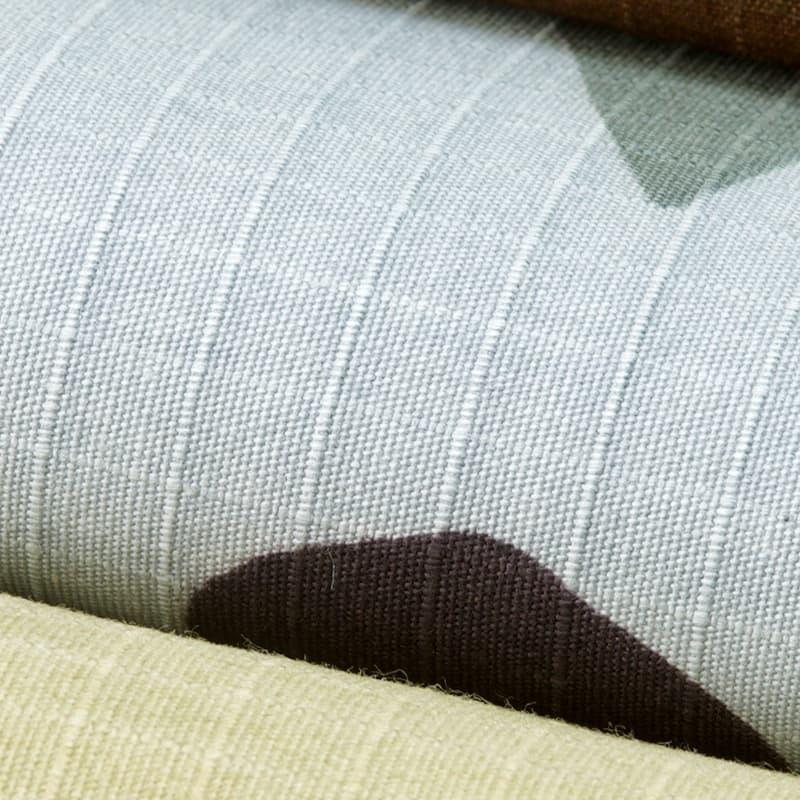
Waterproof Camouflage Coating Fabric